O Princípio de Pareto na Manutenção
O princípio de Pareto, também conhecido como regra 80/20 ou diagrama ABC, refere que 80% das consequências são provocados por 20% das causas. Teve origem num estudo realizado pelo Italiano “Vilfredo Pareto” em 1897,que concluiu que em Itália 20% da população era proprietária de 80% das terras.
Posteriormente verificou-se que este principio tinha aplicação em diversas áreas, desde o mundo dos negócios, ao das atividades profissionais e mesmo pessoais, como por exemplo: 80% da faturação das empresas vem de 20% dos clientes, 20% do trabalho diário gera 80% dos resultados, 80 % do nosso tempo livre passamos com 20% dos nossos amigos, entre outros, razão pela qual este princípio é tão utilizado nos dias de hoje e é considerado uma das 7 ferramentas da qualidade.
Diagrama ABC
O diagrama ABC resultou de um desenvolvimento do diagrama de Pareto, que agrupa os resultados obtidos em 3 classes (A B C) de acordo com o seguinte raciocínio:
-
- Classe A – Os 20% dos resultados de maior significado;
-
- Classe B – Os 30% dos resultados intermédios;
-
- Classe C – Os 50% dos resultados restantes;
As percentagens referidas são indicadores de referência, os valores podem variar de acordo com o estudo em causa.
O princípio de Pareto pode ser aplicado na manutenção???
Se refletirmos sobre esta questão facilmente podemos considerar que este princípio também se aplica em diversas áreas da manutenção, como por exemplo:
-
- 20% dos activos de manutenção são responsáveis por 80% das paragens;
-
- 20% do stock corresponde a 80% dos custos de armazém;
-
- 20% do tempo utilizado em planeamento pode poupar 80% do tempo de execução;
-
- 20% dos clientes da manutenção são responsáveis por 80% dos pedidos;
Se conseguirmos identificar 20% das causas que provocam 80% dos efeitos e nos focarmos nelas vamos tornar o trabalho da manutenção mais eficiente e obter resultados mais significativos do esforço desenvolvido.
Exemplo da aplicação
Admitindo que pretendemos analisar mensalmente os tempos de paragem por avaria de uma linha de produção com 10 equipamentos.
1º Passo
Registar diariamente, durante um mês, os tempos de paragem da linha e identificar o equipamento que a provocou.
Os dados recolhidos estão apresentados na seguinte tabela:

2º Passo
Criar uma tabela com os resultados obtidos de forma decrescente, calcular as percentagens referentes a cada equipamento e a percentagem acumulada.
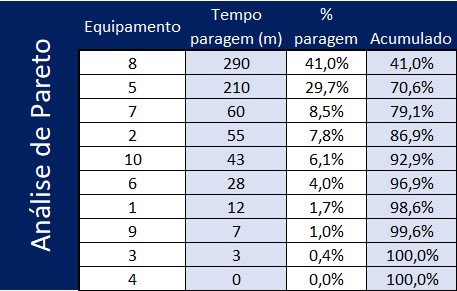
3º Passo
Analisando as duas últimas colunas para definir quais são os equipamentos que têm mais influência na disponibilidade da linha, verificamos que os equipamentos 8 e 5 provocaram 70,6 % do tempo de paragem da linha, confirmando neste caso o princípio de Pareto que 20% dos equipamentos provocam 70,6% das paragens.
Posteriormente definem-se as 3 classes de equipamentos atendendo à criticidade dos mesmos na disponibilidade da linha, concluindo facilmente que os equipamentos 8 e 5 ficam na classe A, os 7, 2 e 10 na classe B e os restantes na classe C.
4º Passo
Desenhar o Gráfico de Pareto.
Após a obtenção dos dados, deve-se focar os recursos existentes a analisar os equipamentos mais críticos (8 e 5) e atuar sobre os mesmos por forma a melhorar a sua disponibilidade, para isso pode-se utilizar ferramentas para identificar a origem dos problemas, como os 5 porquês, formulário 3C, A3, entre outras. Após definir as causas deve identificar as contramedidas que podem reduzir os tempos de paragem da linha e implementar um plano de ação com responsáveis e data por cada ação.
Conclui-se assim, que a utilização deste método permite identificar com facilidade quais são os ativos que tem maior impacto na indisponibilidade da instalação e focar os recursos existentes nos mesmos, de forma a reduzir significativamente os problemas existentes. Deste modo, o gestor da manutenção consegue utilizar de forma mais eficiente os meios que tem disponíveis e obter resultados significativos com maior rapidez e eficiência.
Com 20% do esforço obtenho 80% dos resultados
A SHR PLUS é uma empresa especializada em gestão da manutenção e gestão de ativos. Temos uma vasta experiencia em Manutenção Industrial que disponibilizamos para apoiar as empresas a melhorar a eficiência dos seus departamentos de manutenção, através da utilização de metodologias Lean.
Os nossos objetivos:
-
- Reduzir custos;
-
- Aumentar a disponibilidade;
-
- Aumentar o ciclo de vida dos equipamentos;
-
- motivação e eficiência das equipas;